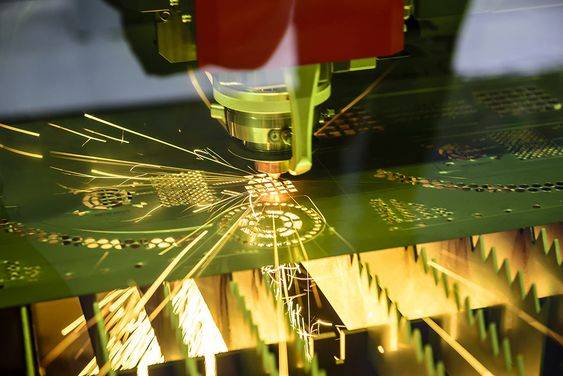
Even though lasers do not work well for every application, they offer efficient use of your material, flexibility, and a controlled process. One of the advantages of using lasers is that they have minimal contact on your material. Because the cut width is so small, you can use them for small radiuses. However, when you are working with laser cutting metal, you may experience a few challenges.
Material Considerations
One challenge that many companies face is the effectiveness of the material. When the thickness increases, the machine does not work well. It depends on power of laser metal cutting machines struggle to cut material of half an inch or thick. The vaporization point, heat conductivity, and surface tension all play a role in the limitations.
When you highly focus your beam and reduce the spot size, you have a sharper cutting tool. For example, by narrowing the spot size from 0.004 to 0.011 inches, you will notice the cutting ability increasing significantly.
Setup Time
If you are cutting an unfamiliar material, the setup time can take a while. Aspects such as the size of the nozzle, assist gas, optical focal length, gas pressure, and speed can all play a role. If you do not set these parameters correctly, you may not be able to cut the material. On the other hand, by properly setting these, you can make your cutting speed even faster.
There are several ways that you can reduce the setup time and maximize your production time for laser cut metal. These include:
- Keep careful records.
- Use a reliable database of parameters and conditions.
- Do similar jobs together.
- Build ergonomic workstations.
- Keep your material next to the laser cutting metal table.
- Use delivery optics that you can easily change.
Distortion Issues
Laser cutting can stress the material more than other methods may. In many cases, however, the process does not generally distort the material too much. However, this depends on the parameters, the composition of the material, and the thickness.
When you work with a thin metal, such as one about 0.001 to 0.005 inches, you are more likely to get distortion. This is because a recast layer can form on the edge of the metal. When the molten material solidifies again, it may cause a warp in your metal piece.
Turn to a Trusted Source for Laser Cut Metal
When you need to work with laser metal cutting, there are many challenges that you may face. These include the type of material and getting the right cut. The good news is that working with the right company can help you mitigate these issues. Weldflow Metal Products is one such company. To learn more about our services, contact us today.